
Examples of several premium A.R.M* Dragline Bucket Wear Parts
are shown below:
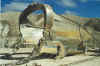 |
A.R.M* Hardfacing has facilitated
significant cost reductions by reducing the qty of production buckets
required to move 14 Million BCM per annum at Blair Athol Coal in Central
Qld. |
|
|
|
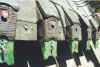 |
A.R.M* Hardfaced Jaw shrouds
can last up to 10 times longer than standard wear parts and usually cost less than double the price of the original part. |
|
|
|
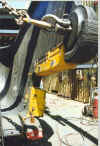 |
The A.R.M* Hardfaced Jaw shrouds
can often be rebuilt twice more from new. This wear package protection
system allows this highly productive bucket to remain in service for up to
9 months at a time without having to perform major maintenance rebuild work in
the field. |
|
|
|
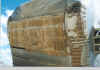 |
This is the new A.R.M* Heel package
shown after 7.5 Million BCM. It has a projected life of 14 Million
BCM or nearly 3 times longer than traditional options. |
|
|
|
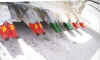 |
The first trial of standard quick tips versus
A.R.M* Hardfaced ones showed a 4 times wear life increase. This was
delivered for only a +30% increase in tip cost. |
|
|
|
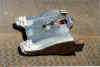 |
This is an example of an A.R.M* Hardfaced
Dragline quick tip after 96,000 BCM. Standard tips were replaced every
10-13 hours. The projected saving per Dragline is around $30,000 a
year ( depending on mine site severity). |
|
|
|
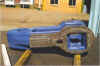 |
Large Drag Shackles have successfully been
A.R.M* Hardfaced. |
|

|